From Rare Bear’s (at this point mythical) 3-blade paddle prop to the new 5-blade MT prop on Clas Thunder I, a new propeller is one of the most visible speed mods on any racer.
With so many different shapes, sizes, and numbers of blades the big question is, “which is fastest?”
The boring, but predictable, answer is it depends, however there are some basic principles that can be applied to every propeller design.
Horsepower
A propeller is just a power converter. It takes the horsepower produced by the engine, and through aerodynamics, converts that power into thrust.
We also must remember two simple but important facts: First there is a maximum limit to how much horsepower an engine can produce. Second, propellers are heavy. Just one of our blades weighs 12lbs, and that’s not including all the weight from the rest of the hub assembly. This means more blades does not always mean more speed. If our propeller is too big, then we end up wasting our hard-earned horsepower trying to spin all that extra weight. On the other hand, a small propeller will move less air and won’t generate as much thrust. These are the kinds of tradeoffs that go into every propeller design.
With all of that being said, during the Gold race in 2019 the engine produced more power than ever before (+900hp), so we definitely had enough to turn a bigger prop. The next task was to determine what this new prop would look like.
Ground Clearance
Actuator Disc Theory says pushing a larger mass of air for a given amount of thrust is more efficient than pushing a smaller mass for the same thrust. It is also ideal that thrust be evenly distributed across the disc circle. Three basic ways to achieve this are: increase the diameter of the blades, increase the number of blades, or increase the number of propellers. Ignoring structural limitations (which as I will cover later is a bad assumption), the simplest solution is to increase the diameter. This might allow you to reuse the old spinner, hub, and hardware. The downside to this approach is increased risk of a prop strike.
This is part of the reason for the F4U Corsair’s inverted gull wing. The airplane was fitted with an R-2800 capable of 2,000hp and taking advantage of all that power meant turning a huge 13ft propeller. But such a large propeller requires tall and heavy landing gear that would be dead weight in a dogfight. So, Vought engineers had the clever idea to bend the wing closer to the ground, which allowed the gear to be shorter and lighter.
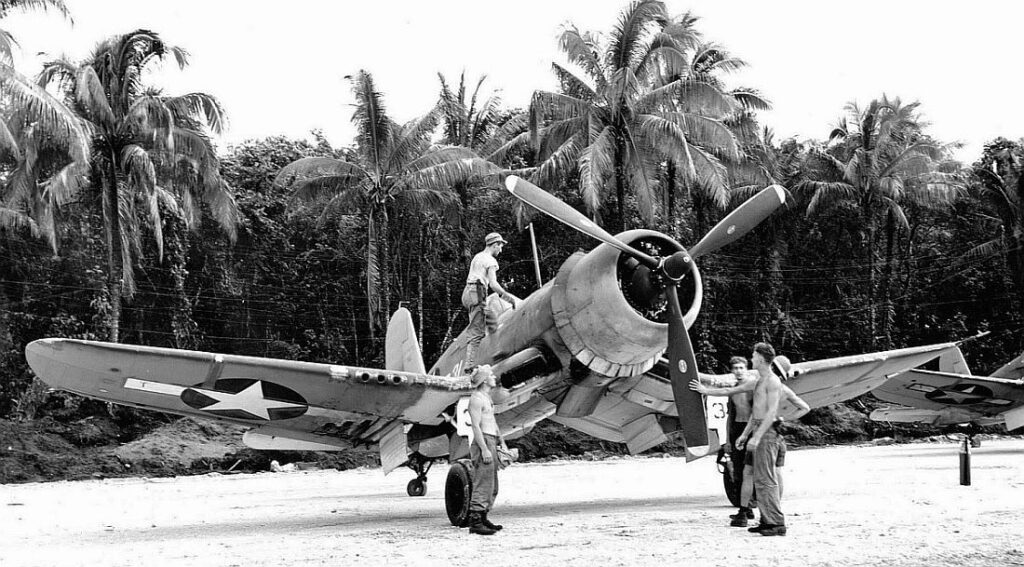
This same philosophy has been incorporated into several modern racers like “Hot Stuff” and “Phantom” where fixed landing gear is required by class rules.
Several of the unlimiteds like Rare Bear with the 4-blade, Czech Mate, and Mr. Awesome pushed their prop diameter so far they had to perform 3 point takeoffs and landings to keep the nose pointed away from the ground.
For Race #30, ground clearance has not been an issue for two reasons: The first is the Legacy nose gear was designed so that if the strut collapsed the prop would still clear the ground. The second reason is something the T-6 class is all too familiar with.
Prop tip speed
For a given RPM, as the prop diameter increases, prop tip speed increases (ie if you double the diameter you double the tip speed).
As the speed of an object increases, so too does the drag. As the speed of an object approaches the speed of sound, the drag increase becomes exponential. This phenomena is what makes breaking the sound barrier so difficult and it’s also why commercial airliners fly slower than they did 20 years ago.
Image source and more in-depth explanation of shockwaves: http://www.aviationchief.com/high-speed-flight.html
Starting around Mach 0.8, the shape of the airfoil at the tip of the propeller will cause the air to go supersonic. But the air only stays supersonic for part of the blade. This means the local air will go from subsonic, to supersonic, and then back to subsonic. The resulting shockwave results in a large energy loss which manifests itself as drag and that loud, familiar crackling sound. At this point, any additional horsepower spent turning the blade faster is only creating noise rather than thrust.
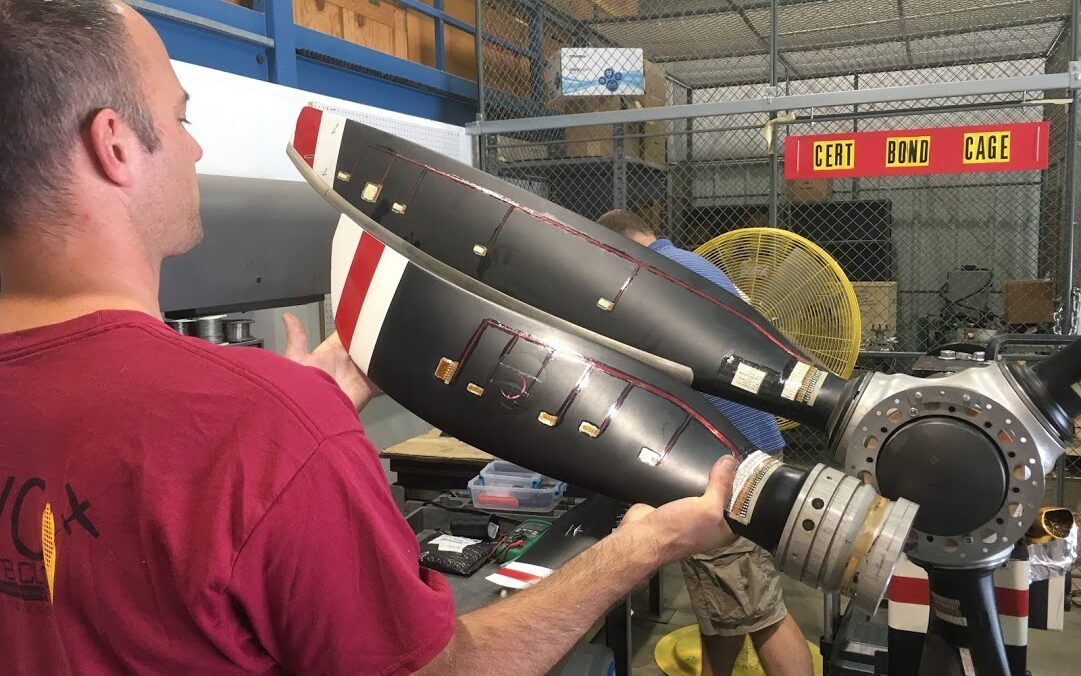
Given that T-6 is a spec class, the teams are prohibited from making any changes to the propeller design. But in Sport Class we don’t have any of those limitations, and for the last several years our prop has been several inches smaller than our competitors with a highly swept tip, to reduce the shock wave. The difference has been audible. Listen to the videos below and notice how much quieter Race #30 is. This isn’t a sign that we are down on power, instead it shows our propeller is generating less drag.
Hub Size
For a fixed pitch propeller, fitting additional blades is relatively easy. There are no independent moving parts and the blades are integrated with the hub.
On the other hand, a constant speed propeller is an intricate assembly of bearings, counter weights, and linkages. Additionally, going from 3 blades to 4 meant the team at McCauley had 33% more components to fit inside the spinner. And for that we needed a bigger hub and spinner.
This worked out well because we needed a larger hub for structural reasons. In 2018 Dave Sterling in Race #8 lost the prop during qualifying and in 2019 a loose propeller forced Lynn Farnsworth out of the gold race. As we’ve been making more and more power, we’ve been diligent to check that the propeller studs don’t back out. The larger hub was designed for a PT6 turboprop and has 8 larger studs instead of the original 6. Fitting this larger hub to the crankshaft requires an adapter and this allowed us to use stronger bolts (180ksi tensile strength) there as well. So in the end the larger hub has given us the room to fit the 4th blade and will ensure the propeller remains attached to the airplane.
Contra Rotating Propellers
LastlLastly, if you have extra horsepower to spin more blades, but you can’t make them bigger and you can’t add more blades to the hub, then the remaining option is to add another hub.
This option brings with it a whole new level of weight, complexity, and stability, which brings us back to the initial issue of ensuring you have enough extra horsepower for it to be worthwhile.
But, with all of the research and testing done during WWII, companies like Rolls Royce and Pratt and Whitney were building bigger, more powerful engines which in turn drove the development of the later model Spitfires, Boeing XF8B, and the Republic XP-72.
Contra rotating propellers will hopefully be returning to the world of air racing in the near future. With the announcement of Air Race E, several teams have released sketches and CAD models featuring a contra rotating configuration.
Conclusion
There is no one-size-fits-all solution when it comes to propellers. Horsepower, weight, airspeed, engine cooling, fuel flow all affect each other and affect the efficiency of a propeller. It is the task of each team to sort through all of these variables and find the best design for their aircraft.
-“Young” Thomas
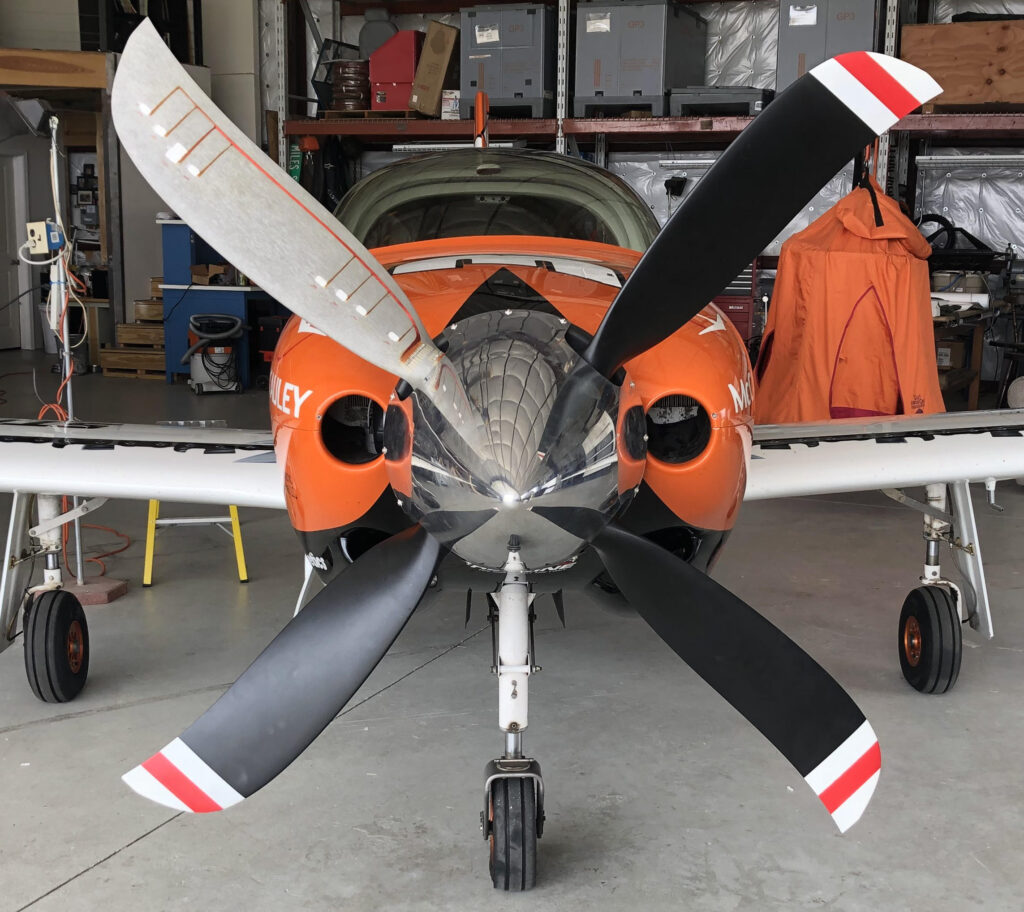